

In 2018 sloeg Produlab Pharma in Raamsdonksveer de eerste paal voor een nieuwe veterinaire non-penicillinefabriek. In samenwerking met aannemer Heembouw en Adcom 2000 Architecten & Ingenieurs realiseerde Kropman Installatietechniek letterlijk alle installaties die nodig zijn voor de productie van diergeneesmiddelen.
Produlab Pharma is een zelfstandige farmaceutische onderneming die zich vanaf 1991 bezighoudt met de productie van diergeneesmiddelen. Het bedrijf is begonnen met één productielocatie waarin penicilline-houdende medicijnen worden gemaakt.
Penicilline is één van de belangrijkste medicijnen van de twintigste eeuw maar heeft ook een probleem: het laat zich niet reinigen. Met andere woorden: sporen van penicilline in een ruimte waar je ze niet wilt hebben, zijn níet te verwijderen. Toen Produlab Pharma dan ook wilde uitbreiden met de productie van geneesmiddelen zónder penicilline, betekende dit zonder enige discussie de bouw van een nieuwe locatie.
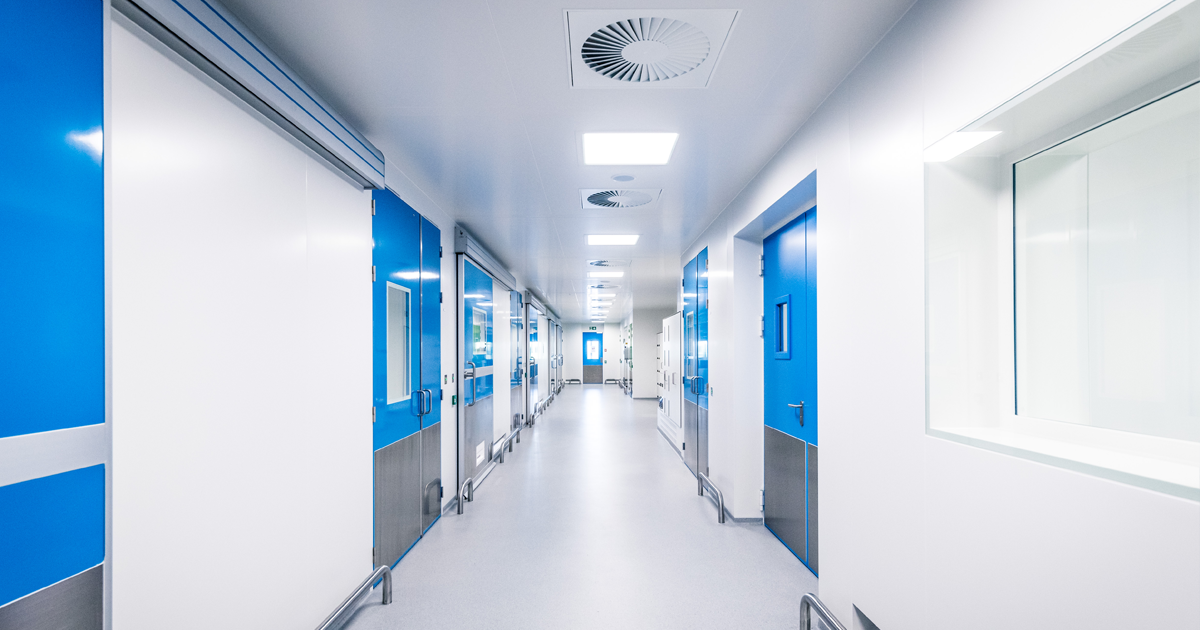
‘Uitdagende en geweldige klus’
Kropman installatietechniek werd voor deze nieuwbouwlocatie benaderd om alle installatietechnische werkzaamheden en de bouw van de productieruimtes te realiseren. Geert van der Vliet is projectmanager en geeft aan: ‘Een serieus uitdagende en hiermee geweldige klus voor een bedrijf dat alle installatietechnische disciplines in huis heeft. En bovendien groot. Het oppervlak van de fabriek beslaat 12.000 m2 bvo, de cleanroom 2.500 m2 en de techniekruimtes 4.100 m2.’
‘En eigenlijk kun je bij de techniekruimtes nog 2.500 m2 optellen omdat zich boven het plafond van de cleanrooms letterlijk uitsluitend installatietechniek bevindt om de ruimtes te conditioneren en vrij te houden van vervuiling. Uiteindelijk heeft Kropman meer dan honderd verschillende systemen gebouwd in deze fabriek.’
Ontwerpen in Revit
Een goede voorbereiding is het halve werk en daarom werden alle installaties eerst uitgewerkt in Revit. In eerste instantie betrof dat een grof ontwerp op basis van de specificaties van de klant en daarna een veelomvattende detailengineering.
Van der Vliet: ‘Ik zou het niet direct een echt BIM-model willen noemen, maar het feit is wel dat alles in 3D is ontworpen waardoor je direct ziet of installaties goed passen en in een later stadium ook nog bereikbaar zijn voor onderhoud.’
Ruim bemeten HVAC-installaties
Qua installatietechnieken maakt Geert van der Vliet een onderverdeling in verschillende systeemgroepen: cleanroom, HVAC, black-utilities, clean-utilities, proces equipment, building management en electrical systems. ‘De meest in het oog springende systeemgroep in deze fabriek is bestemd voor de cleanrooms waar de vereiste reinheidsklasse extreem hoog moet zijn. Hierdoor zijn de bijbehorende HVAC-installaties op z’n zachtst gezegd nogal ruim bemeten om de lucht te kunnen produceren die nodig is voor het realiseren van reinheidsklassen GMP A tot en met C.’
Een tweede type installaties betreft de ‘clean utilities’. Dit zijn de systemen die een rol spelen in zowel de productie- als de reinigingsprocessen (CIP, COP en SOP). Zij produceren onder andere injectievloeistoffen, ultraschoon water en ultraschone stoom. Als derde noemt Geert van der Vliet de ‘black utilities’; de pure W-installaties die stoom, warmwater, koelwater en gekoeld water produceren.
Deze media zijn voornamelijk bedoeld voor het verwarmen, koelen en steriliseren van tanks die in de productie worden gebruikt. Maar ook voor de verwarming en koeling van productieruimten. Daarnaast behoren tot de black utilities ook de installaties die vacuüm en perslucht produceren voor de productieprocessen.
Procesinstallaties en regeltechniek
Vervolgens heeft Kropman een rol gespeeld in de procesinstallaties waar de daadwerkelijke productie van medicijnen plaatsvindt. Bij deze fabriek gaat het om 3 vaste tanks met een inhoud van 2.000 liter en 30 mobiele tanks met een inhoud van 500 liter.
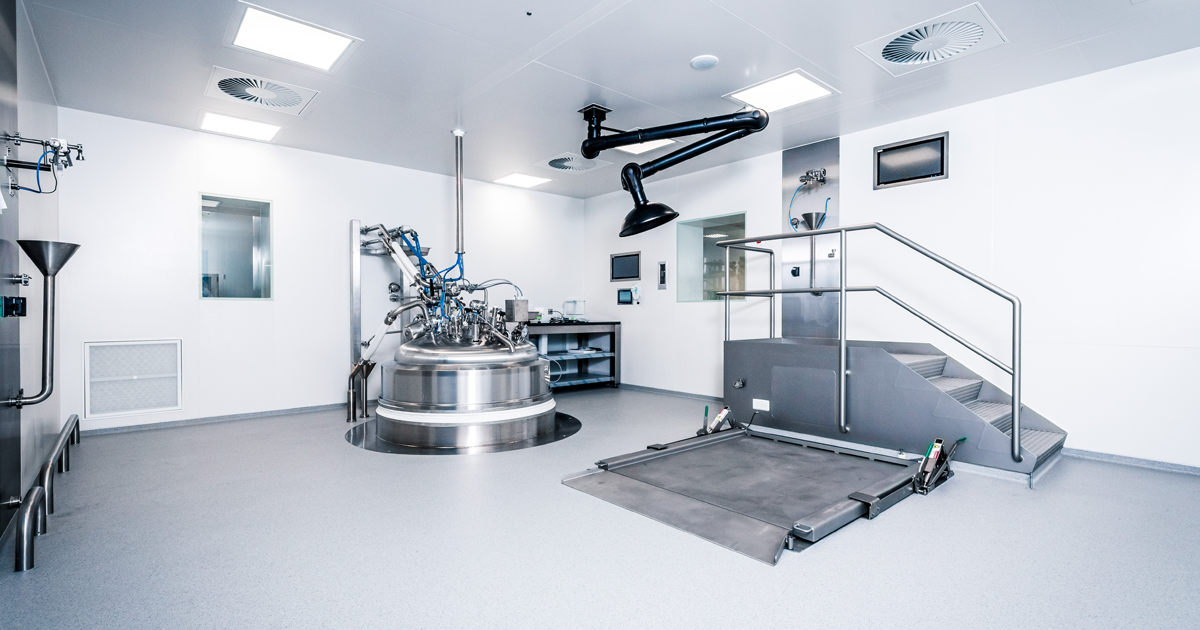
Deze tanks zijn aan 1 van de 20 zogeheten vessel docking stations te koppelen waar zij de juiste ingrediënten in de juiste hoeveelheid ontvangen. Naast een grote stoominstallatie, zoals eerder genoemd, is specifiek voor de productieprocessen ook een zeer ruim bemeten koelinstallatie gerealiseerd.
Tot slot verzorgde het bedrijf ook de meer gangbare installatietechniek zoals het aanleggen en aansluiten van alle elektra, de verlichting, het brandmeldsysteem, inbraakbeveiliging enzovoorts. De automatisering van HVAC en black-utilities viel geheel onder de verantwoordelijkheid van Kropman. Voor de automatisering van de clean-utilites en proces equipment heeft Kropman alle hardware gebouwd. De software van deze systemen werd door een gespecialiseerde partij geleverd, een ‘plant wide’ SCADA-systeem.
Documenteren
Van der Vliet: ‘Het ontwerpen en realiseren van deze uiteenlopende installatietechnieken is ons dagelijks werk. Wat dit project echter extra zwaar en complex maakte, is het feit dat je bij de bouw van een fabriek voor medicijnen alles moet documenteren om aan de GMP-richtlijnen te voldoen.’
Hij vervolgt: ‘Dat betekent dat je vanaf het moment dat je met je ontwerp aan de slag gaat, alles moet vastleggen. Niet alleen hoe je het gedaan hebt en waarom je bepaalde keuzes hebt gemaakt, maar ook welke testen je hebt gebruikt om aan te tonen dat je aan gevraagde eisen voldoet, wat de testresultaten zijn enzovoorts. Een monsterklus.’
1 mei was de contractuele opleverdatum waarmee een uitgebreide SAT (Site Acceptance Test) van enkele maanden succesvol werd afgerond. ‘We zetten nu de laatste puntjes op de i. Zo moeten we nog een conformiteitsverklaring afgeven en enkele laatste zaken nalopen, maar dan kan de fabriek officieel gaan opstarten. Trots? Jazeker!’
Fotografie: Istar Verspuij.
Heb jij ‘n tip voor deze rubriek? Stuur je suggestie naar demakersvanmorgen@technieknederland.nl!